Advanced Compressed Air Solutions Featuring Superior Air Dryers
Enhance Equipment Longevity and Optimize Performance with Refrigerated or Adsorption (Desiccant) Air Dryers
The Importance of Implementing a Compressed Air Dryer.
A compressed air dryer is an essential piece of equipment specifically engineered to extract water vapor and moisture from industrial process air. Its key role is to efficiently separate and eliminate water vapor from compressed air systems, thereby preventing condensation and mitigating potential damage to equipment, tools, and processes that depend on dry compressed air.
Impacts of using air dryers
- Cooling air to facilitate the condensation of water vapor
- Effectively separating condensed water from the airflow
- Mitigating corrosion in pipelines, valves, and pneumatic systems
- Enhancing equipment performance and reliability
- Minimizing maintenance costs and reducing downtime
- Improving product quality across industries such as food, electronics, and pharmaceuticals
- Boosting the energy efficiency of compressed air systems
- Prolonging the lifespan of pneumatic tools and equipment
Refrigerated Air Dryers
Refrigerated air dryers, akin to residential air conditioning systems, function by cooling compressed air to condense and effectively eliminate moisture.
- Utilize cool air at approximately 40°F to facilitate moisture condensation
- Employ mechanical separation to extract water droplets
- Achieve typical dew points around 3°C
- Well-suited for a range of industrial applications
- Demonstrates enhanced energy efficiency for moderate drying requirements
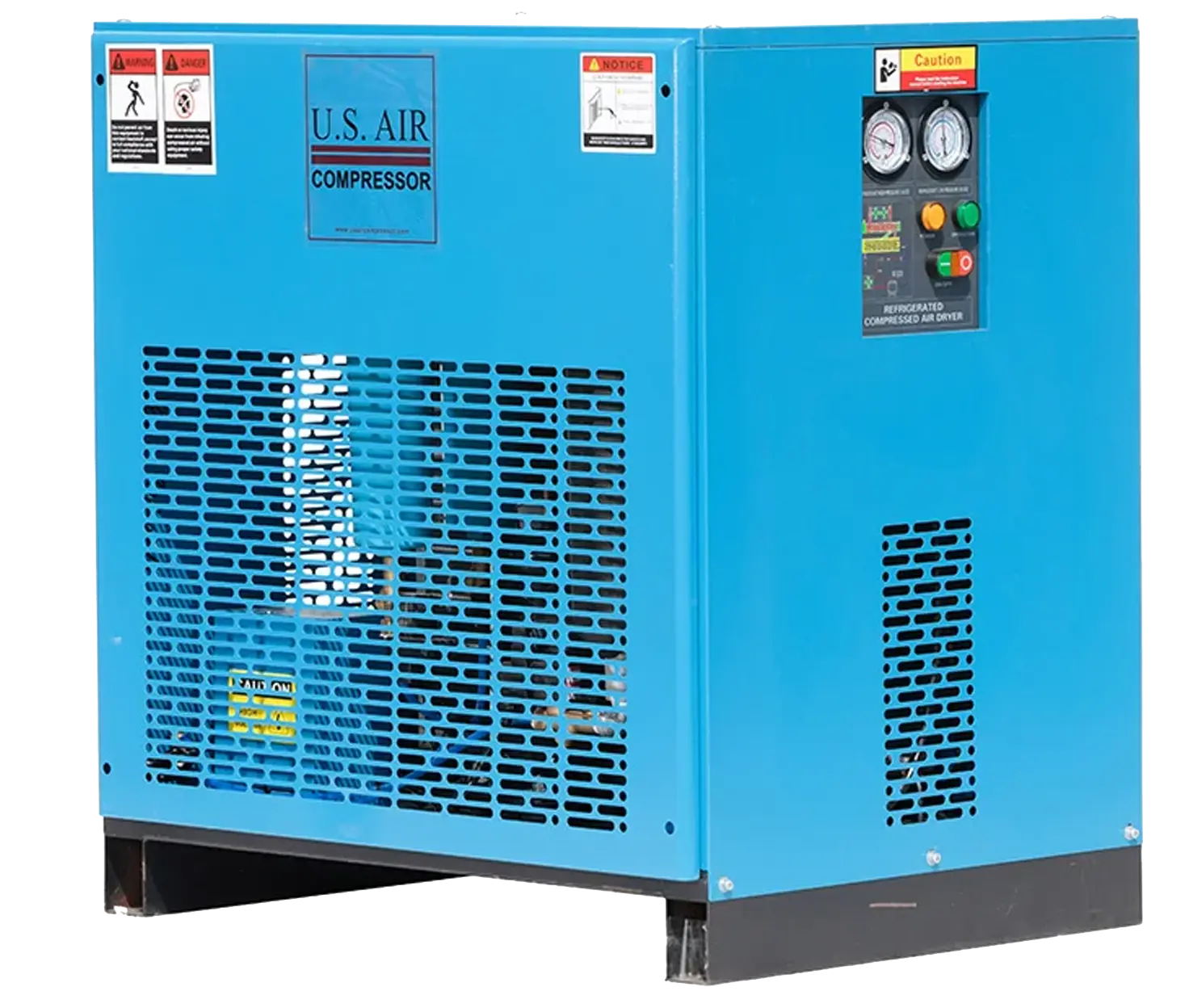
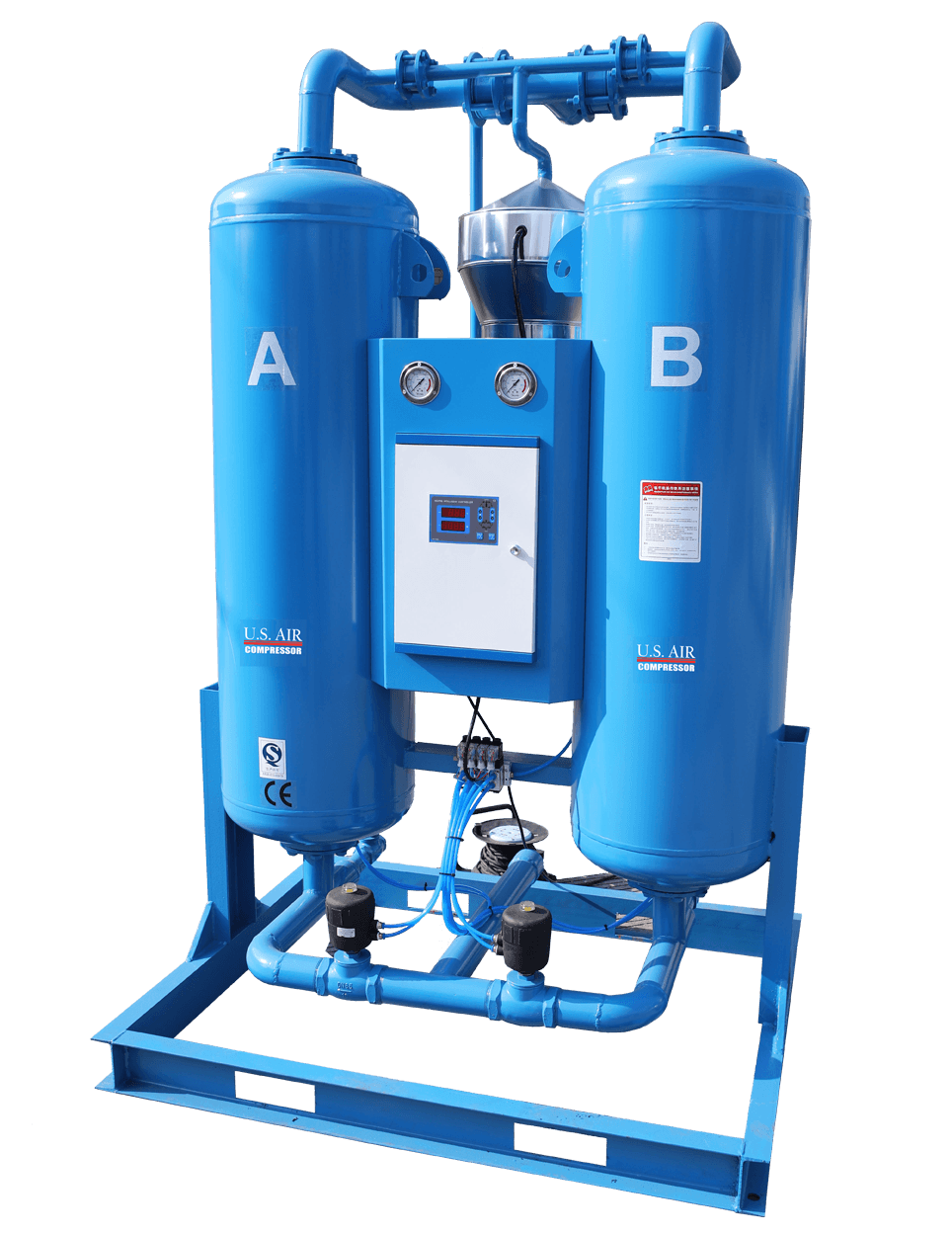
Adsorption (Desiccant) Air Dryers - Heatless
Heatless desiccant air dryers effectively eliminate moisture from compressed air through the utilization of desiccant materials such as activated alumina or silica gel.
- Employ pressure swing adsorption technology for optimal regeneration efficiency
- Utilize compressed air for the regeneration process, generally consuming 15-20% of dried air
- Features a refined design that minimizes initial investment costs
- Demonstrates superior energy efficiency regarding power usage
- Well-suited for challenging environments, remote locations, and hazardous areas
- Promotes simplified maintenance due to a reduced number of components
- Suitable for operations with limited hours or functioning as backup systems
- Able to achieve exceptionally low dew points
Adsorption (Desiccant) Air Dryers - Heated
Heated desiccant air dryers effectively eliminate moisture from compressed air by directing it through a tower containing desiccant materials, such as activated alumina or silica gel.
- Utilize external heat sources for efficient desiccant regeneration
- Increased energy demands due to the heating process
- Higher initial investment required for components such as heaters and blowers
- Optimized for large-scale industrial applications
- Deliver enhanced drying capacity and efficiency
- Demand more frequent maintenance owing to their complex components
- Can achieve approximately 40% greater cost-effectiveness over a 10-year lifespan
- Adapt to both flow and moisture load reductions, facilitating significant energy savings
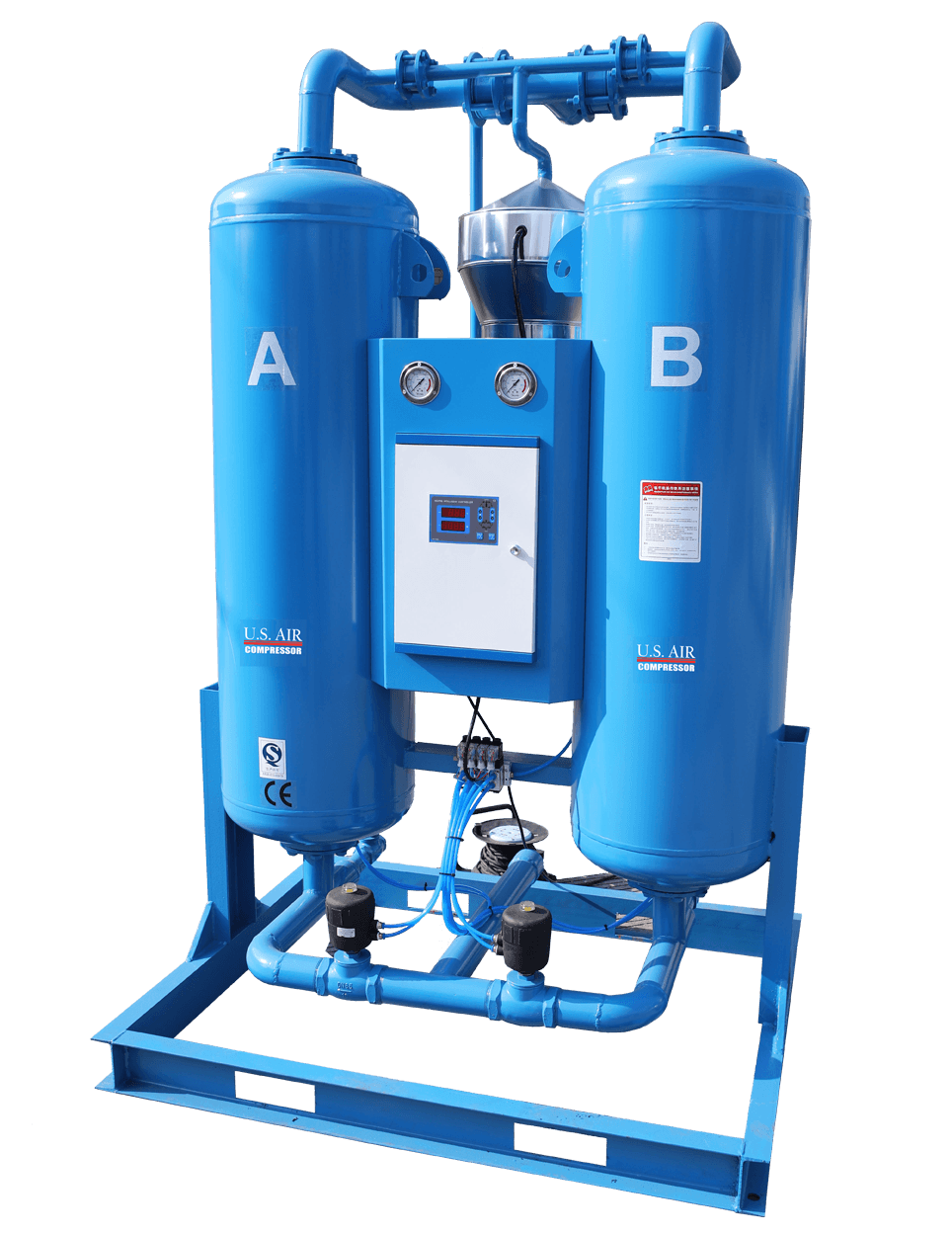
Key Considerations
The following considerations are essential for the selection of a compressed air dryer that will efficiently eliminate moisture, uphold system effectiveness, and align with your specific operational requirements.
Air Quality Requirements
Identify the necessary dew point and air purity standards pertinent to your specific application. This assessment will aid in selecting between refrigerated dryers (suitable for moderate drying needs) and desiccant dryers (ideal for stringent dry air requirements)
Operating Conditions
It is essential to consider the ambient temperature, inlet air temperature, and pressure of your compressed air system. These parameters have a substantial effect on dryer performance and efficiency. For instance, a 20°F increase in inlet air temperature can potentially double the water load on a dryer.
Flow Rate and Capacity
Confirm that the dryer's flow rate is compatible with your compressor's output.. The dryer must be appropriately sized to accommodate the maximum capacity of your air compression system, generally measured in CFM at 100 PSI.
Ready to dive into the world of air power?
Rest assured, you’re in great hands with a company dedicated to creating smart, efficient compressors that work as hard as you do, all backed by a reliable 10-year warranty
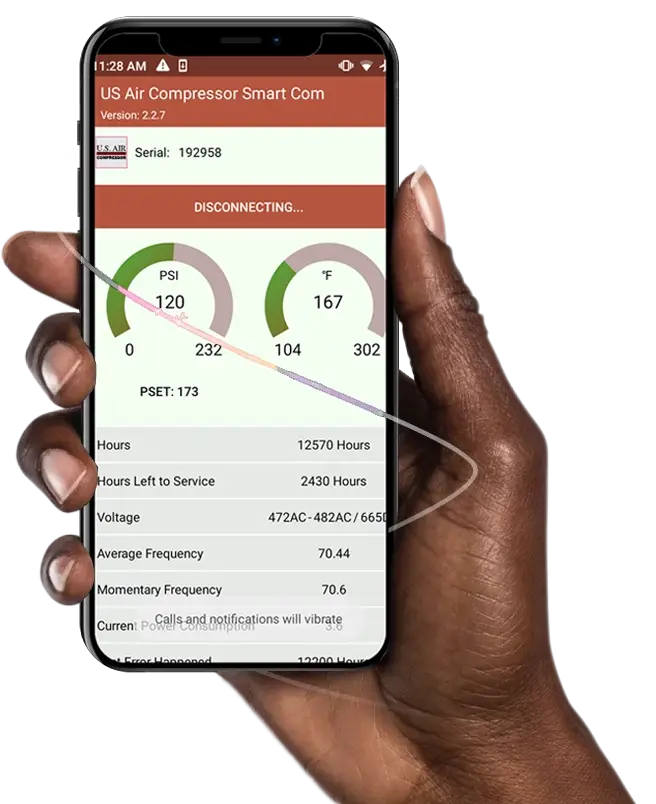